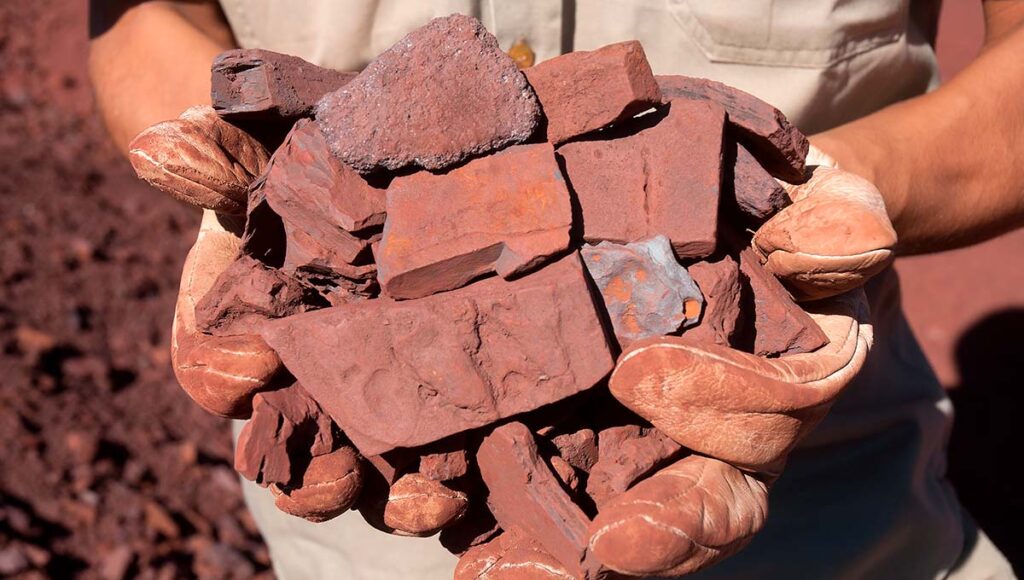
Company aiming to create oxygen on moon finds process to make steel plants cleaner
Steel, known for its strength and versatility, is integral to modern infrastructure, from skyscrapers to everyday household items. However, the traditional steel industry is a significant contributor to global greenhouse gas (GHG) emissions, accounting for approximately 7-10% of the total. This environmental impact, combined with declining ore grades and the high cost of existing green technologies, has catalyzed the search for more sustainable solutions. Among these, the Helios Cycle™ emerges as a pioneering technology, offering superior unit economics and environmental benefits.
The Problem and Opportunity in the Steel Industry
The steel industry’s importance to the global economy is immense, with an annual production of nearly 2 billion metric tons valued at approximately USD 1.6 trillion. However, this sector faces several critical challenges:
The Problem and Opportunity in the Steel Industry
The steel industry’s importance to the global economy is immense, with an annual production of nearly 2 billion metric tons valued at approximately USD 1.6 trillion. However, this sector faces several critical challenges:
- Declining Iron Ore Grades: The depletion of high-grade iron ores forces steelmakers to rely on costly beneficiation processes, driving up production costs.
- Carbon-Intensive Processes: Traditional steelmaking methods, such as blast furnaces and direct reduced iron (DRI) processes, are highly polluting.
- Economic Viability of Green Alternatives: Emerging green technologies like hydrogen-based DRI and electrolysis are not yet economically viable for widespread industrial adoption.
- Regulatory and Market Pressures: Carbon taxes and environmental, social, and governance (ESG) policies further erode the profit margins of steelmakers.
These challenges create an urgent need for innovative and economically viable green steel solutions.
Alternatives to Decarbonize the Steel Industry
- Hydrogen-Based Direct Reduced Iron (H2-DRI): This technology uses hydrogen instead of carbon as a reducing agent, producing water vapor instead of CO2. Notable projects include SSAB’s HYBRIT initiative and H2 Green Steel in Sweden. Although promising, H2-DRI faces challenges related to the high cost of green hydrogen production and the need for substantial infrastructure investment.
- Carbon Capture, Utilization, and Storage (CCUS): CCUS technologies aim to capture CO2 emissions from steel production processes and either store them underground or repurpose them for industrial applications. Projects like the ArcelorMittal’s carbon capture initiatives demonstrate the potential of CCUS, though high costs and energy requirements remain significant barriers.
- Molten Oxide Electrolysis (MOE): Companies like Boston Metal are developing MOE technology, which uses electricity to separate iron from its ore without carbon emissions. However, MOE is still in the pilot stage and requires substantial energy inputs, making it less viable for immediate large-scale implementation.
- Increased Scrap Usage: Recycling steel scrap in electric arc furnaces (EAF) is a well-established method to reduce emissions. This approach is limited by the availability of scrap metal and the quality of steel that can be produced from recycled materials.
- Utilizing renewable energy sources to power steel production processes can significantly reduce the carbon footprint. This strategy is particularly relevant for technologies like H2-DRI and MOE, which require large amounts of electricity.
Key Advantages of the Helios Cycle™
- Indifference to Ore Grade: Unlike traditional methods, the Helios Cycle™ can process a broad spectrum of iron ore grades, including low-grade ores (50-62% Fe) and tailings (less than 50% Fe). This flexibility eliminates the need for expensive high-grade ores.
- Zero Carbon Emissions: The Helios Cycle™ produces zero direct carbon emissions, compared to the significant CO2 output of blast furnaces and DRI technologies.
- Cost Efficiency: Operating at temperatures between 250°C and 550°C, the Helios Cycle™ is more energy-efficient and cost-effective. The expected operating cost is $250-$350 per 1000 kg of iron, significantly lower than traditional methods.
- Modular and Flexible: The modular design of Helios furnaces allows for easy integration into existing production lines and can be deployed at mining locations, reducing transportation costs and associated emissions.
In Conclusion
The challenges facing the steel industry—declining ore grades, carbon-intensive processes, and economic pressures—are driving a critical shift toward sustainable solutions. Technologies like Hydrogen-Based Direct Reduced Iron (H2-DRI); Carbon Capture, Utilization, and Storage (CCUS); and Molten Oxide Electrolysis (MOE) offer promising pathways to reduce emissions and enhance efficiency, However, each faces hurdles such as high costs and scalability issues.
Amidst these innovations, the Helios Cycle™ offers superior unit economics and environmental benefits. As the steel industry navigates the pressures of sustainability and economic viability, Helios stands out as a leading solution poised to drive the transition to a greener future.