Home / Our Solutions / Lunar Oxygen
Reforging the
Lunar Oxygen
Refueling in space
Oxygen mining on the Moon
The capability to mine oxygen directly on the Moon is a game changer for space exploration. That’s because transporting materials from Earth to the lunar surface costs hundreds of thousands of dollars per kilogram, rendering long-term missions economically impractical. This high cost is largely due to the tyranny of the rocket equation which refers to the exponential increase in fuel needed for a rocket as it increases its velocity, making space travel extremely challenging and inefficient due to the need to carry additional fuel to propel the extra fuel itself. By sourcing oxygen on the Moon which makes up 75% of the total rocket mass, we can drastically reduce these expenses and make sustained lunar missions feasible.
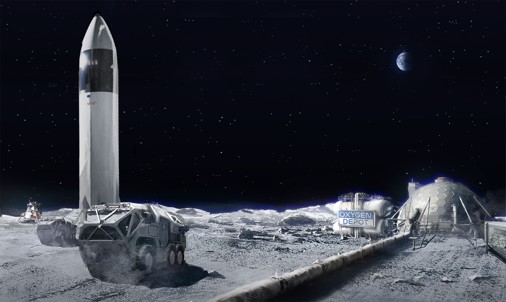
Oxygen mining on the Moon
Helios is developing technologies to extract oxygen from lunar regolith, the mixture of powdery dust and broken rock on the moon’s surface. This process provides rocket fuel oxidizer, dramatically reducing the cost of future space activities.
(Mass percentage of various elements on the lunar surface)
Approximately 45% of the soil mass of the moon is made of oxygen.
Core Technology
Molten Regolith Electrolysis (MRE) Reactor
The MRE Reactor is the heart of the Helios system: By melting and electrolyzing the abundant oxides scattered across the lunar surface, the reactor efficiently separates them into oxygen and essential metals such as iron, aluminum, titanium, and others.
Economic Potential
Producing oxygen on the Moon will significantly reduce the launch mass from Earth, eliminating the need to supply terrestrial oxygen beyond Low Earth Orbit (LEO). This lunar-derived oxygen can be used on the moon’s surface, in cislunar space, or for trans-Mars injections, at substantial cost savings. By enabling these advancements, lunar oxygen production will pave the way for a more sustainable future for humanity beyond Earth.
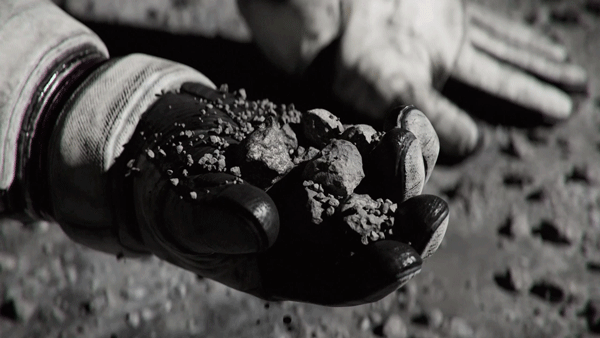
The long-term vision of space mining
Eliminating the need for fossil fuels requires a lot of metals and minerals. We can approximate the total amount of materials needed for a sustainable earth by estimating the needed new solar panels, batteries, electrical vehicles, geothermal and nuclear plants, dedicated infrastructure and so on.
We can try to minimize these discrepancies with new technologies but the only way to really solve this problem is to get these resources from beyond earth, mining the moon and near-earth asteroids. There is an abundance of materials in space, which will easily satisfy our needs for the foreseeable future. Helios is developing technology to drastically reduce space flight costs bringing us closer to an economically viable space mining future.
The quantity of raw materials needed to transition to a fully sustainable life on earth, compared to all the known raw minerals that exist on earth, which are simply not enough. (reference article)
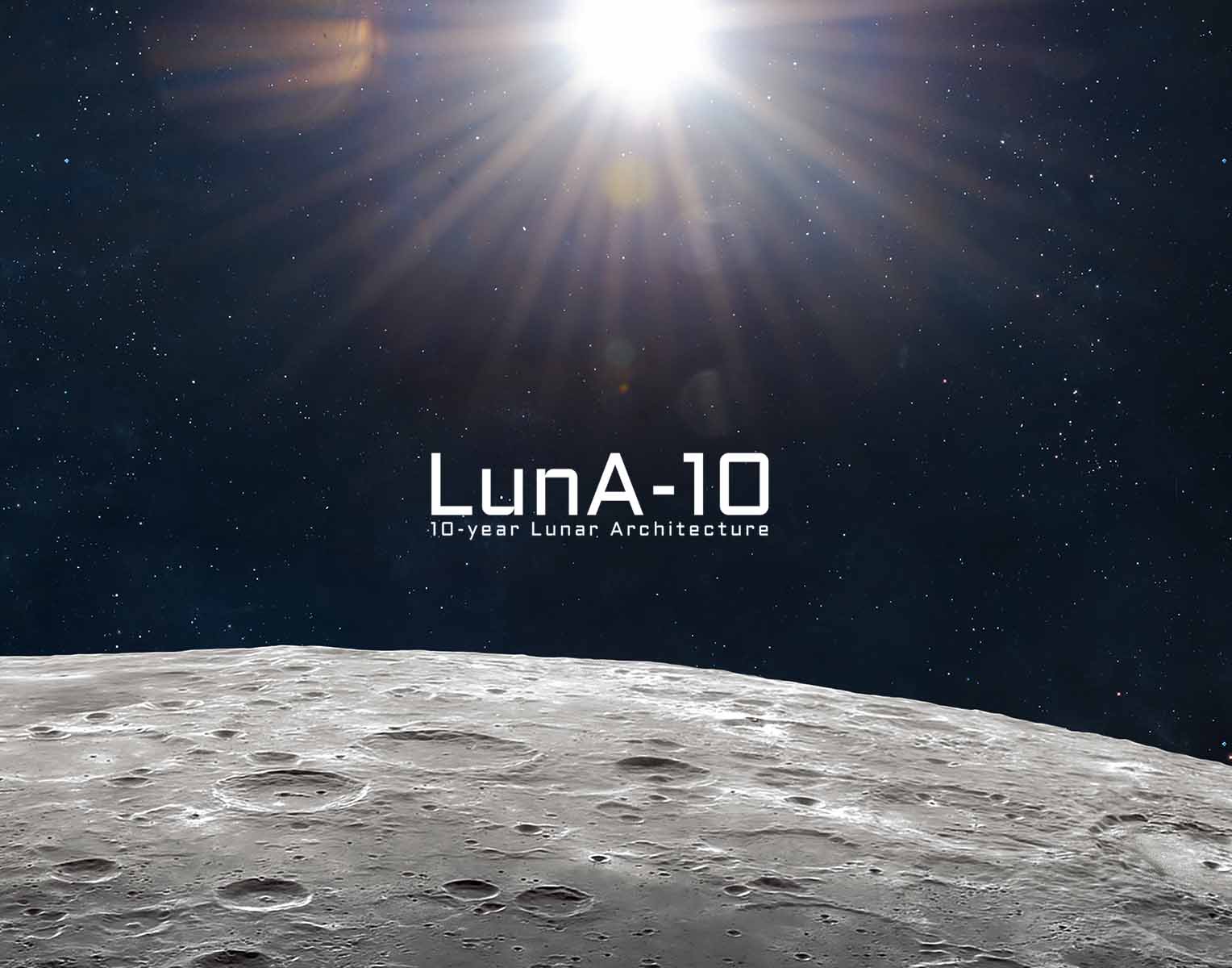
Helios cooperation with DARPA
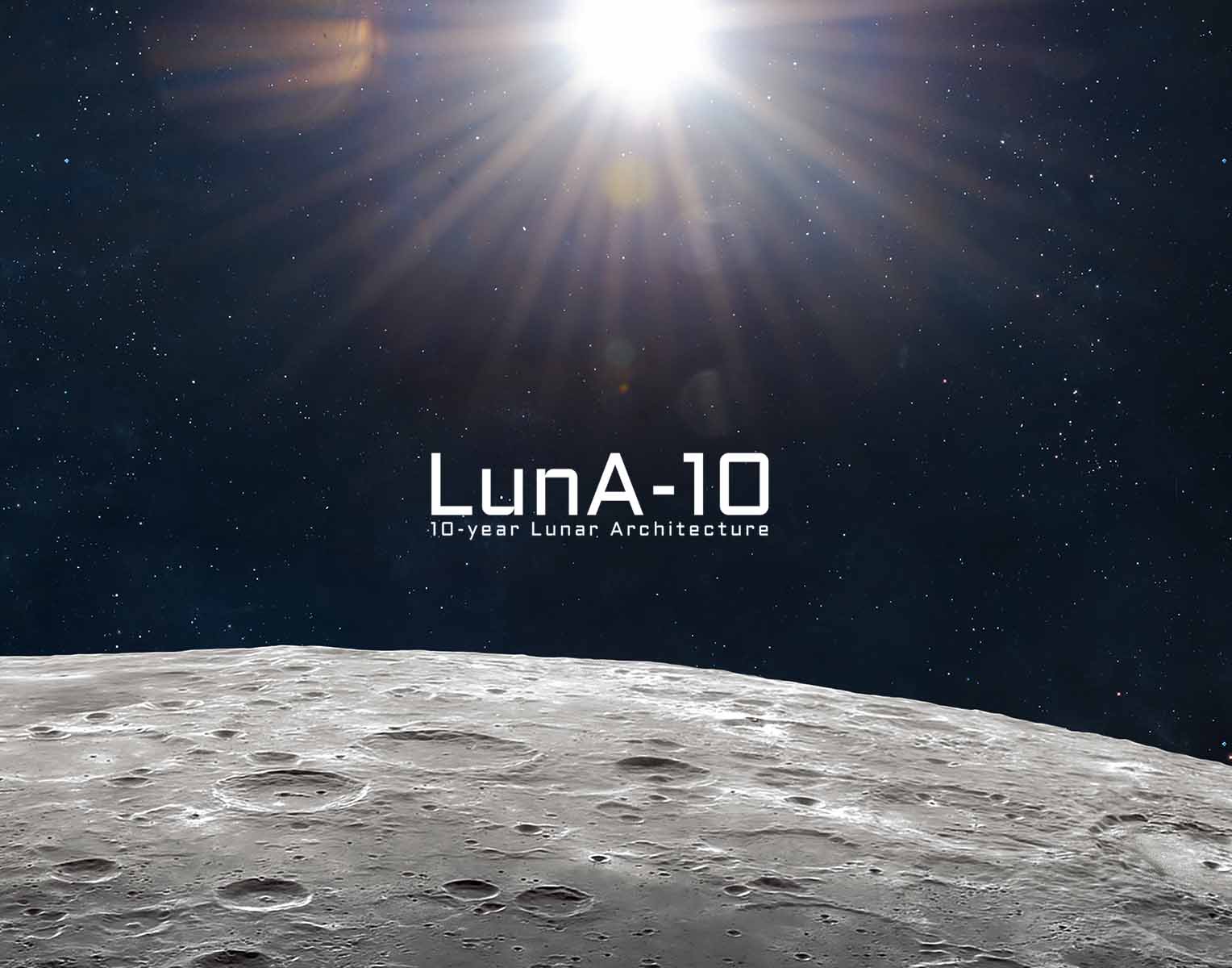
Learn more about what Helios can do for earth and beyond
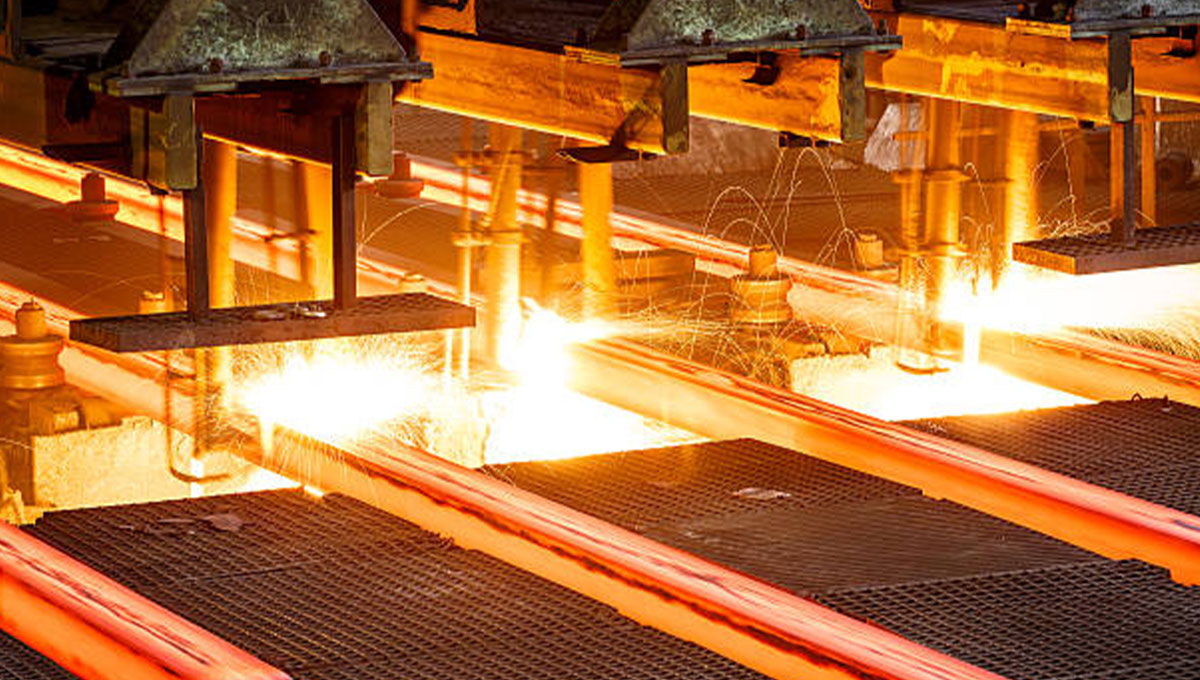
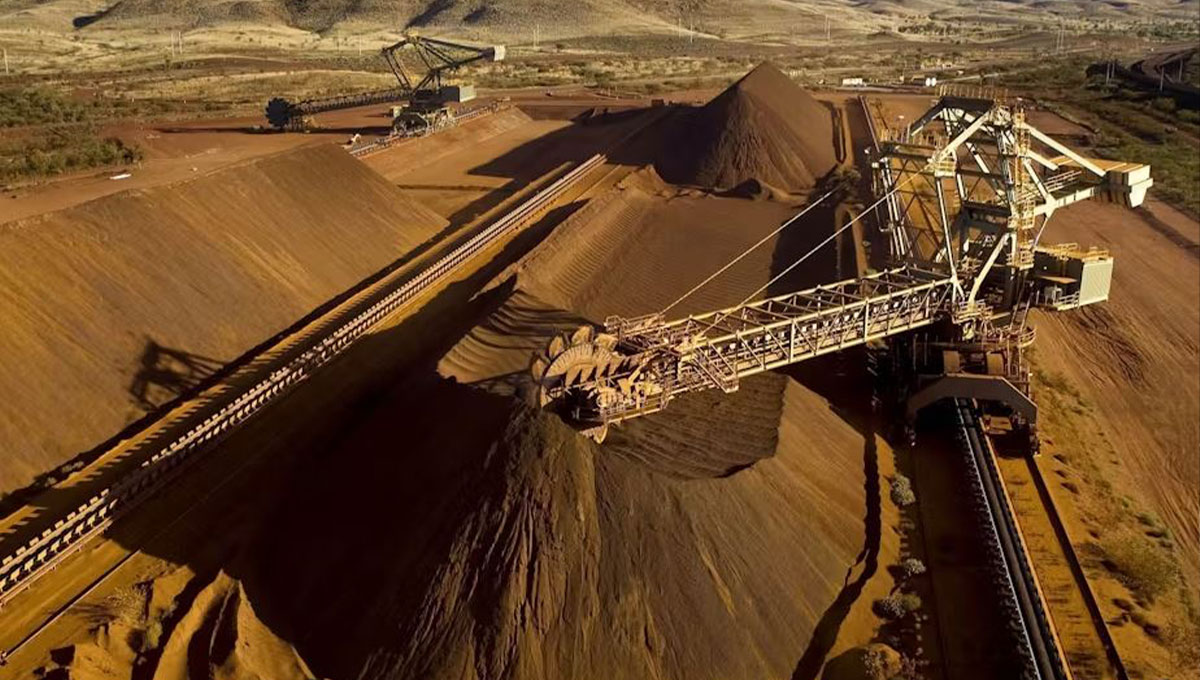
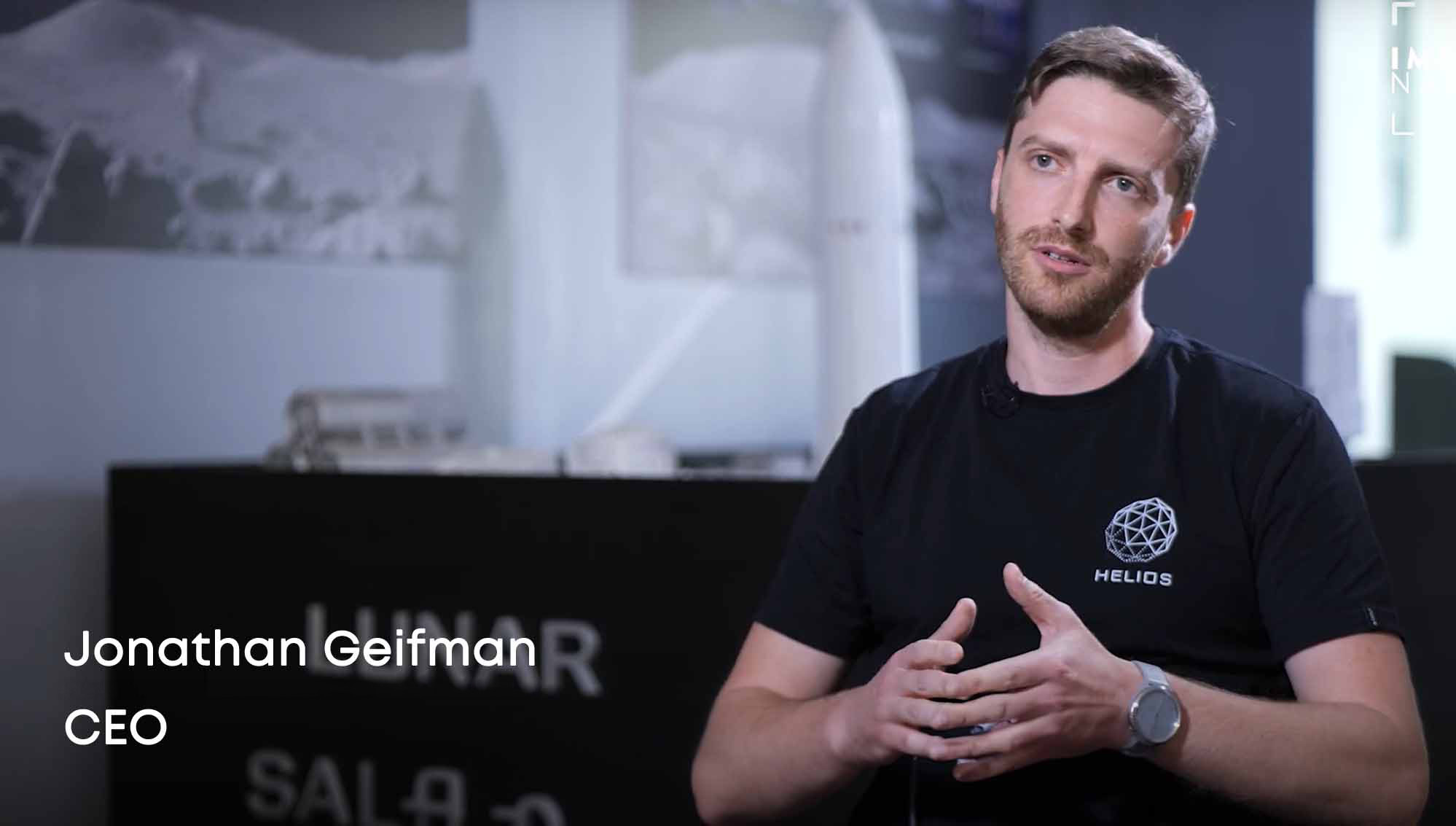
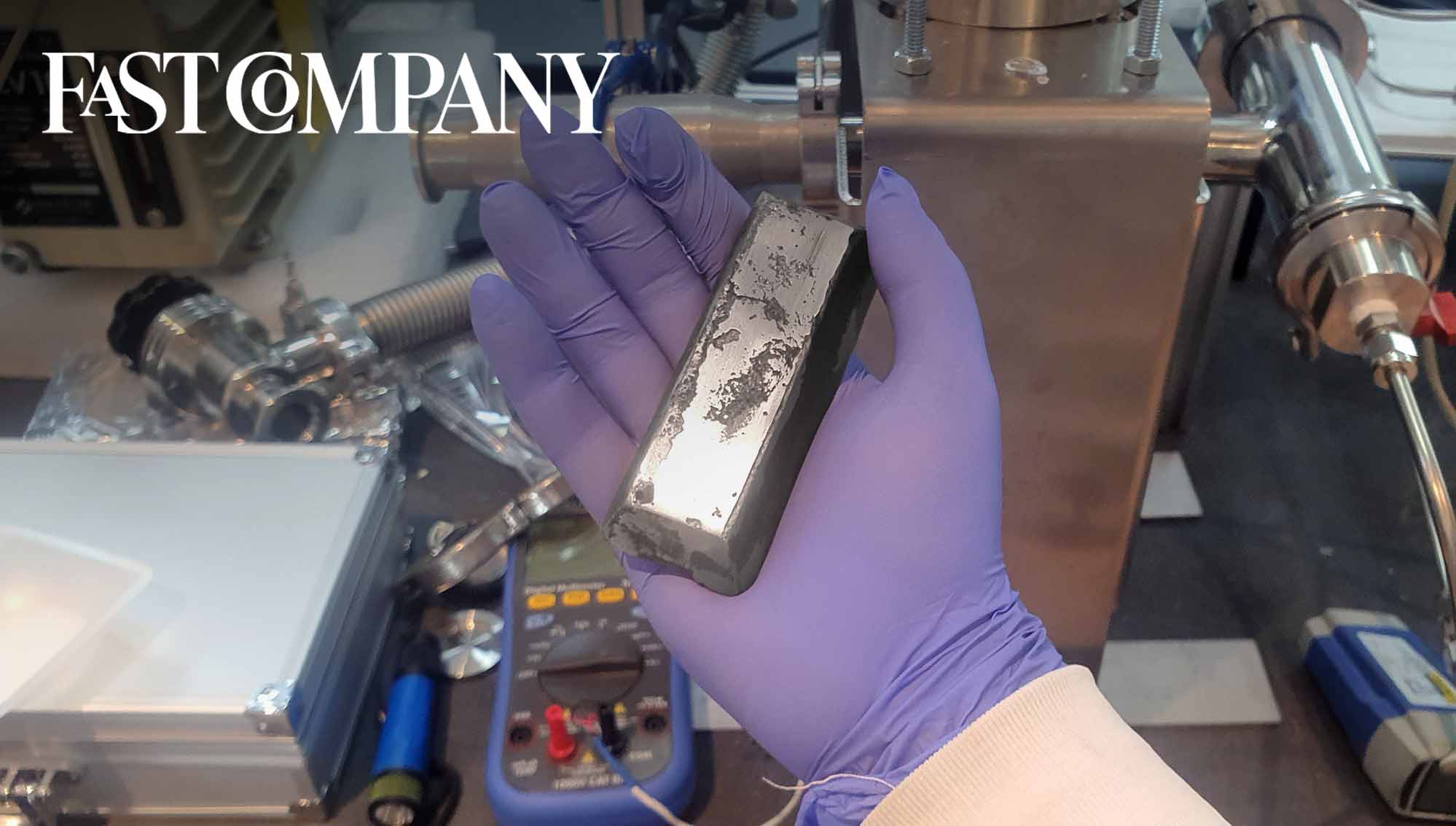
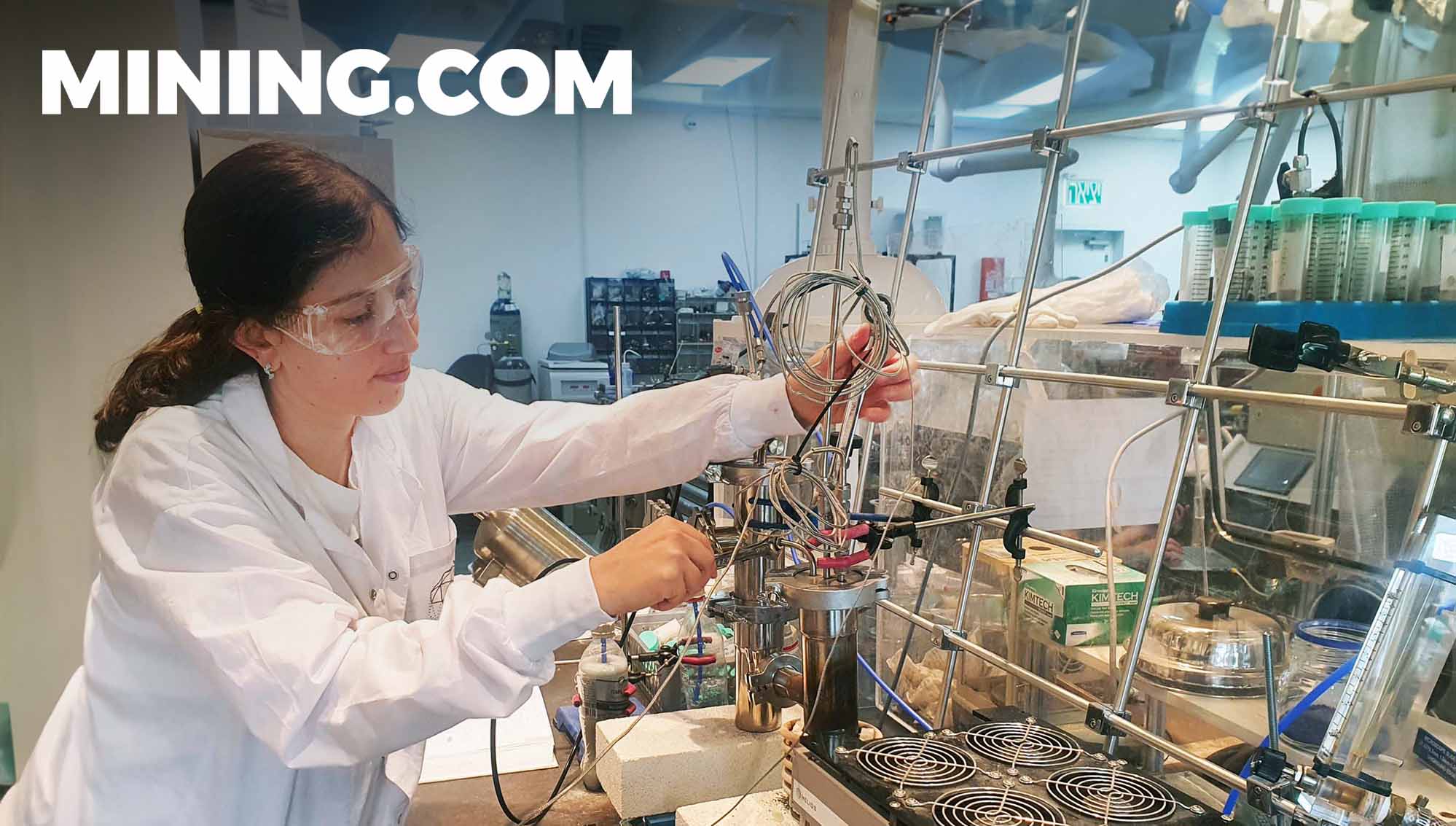
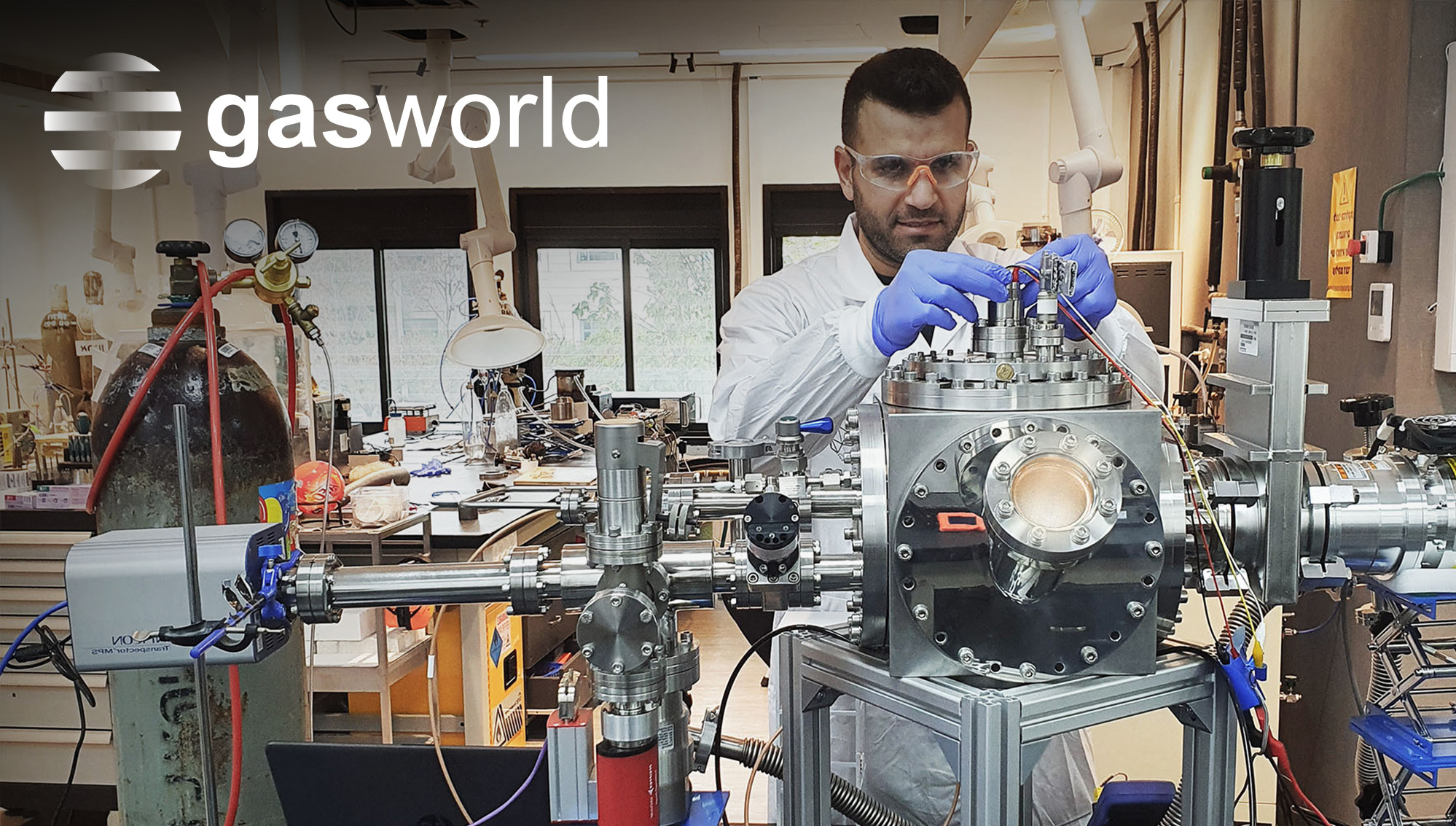